2025-07-02
A discussion on digital innovation, digital sovereignty and future competitiveness
We are approaching this year's summer break in Scandinavia and before the holidays begin, I am writing down some reflections from some of the events, feelings and facts that have characterised my ‘spring season’.
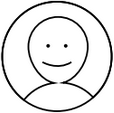
Written by Susannah Eriksson